The tool changes the process to a certain extent. As a tool for needles and brains, if we understand its performance and use it correctly, and then improve the machining technology and increase the processing efficiency, it can bring great benefits to the enterprise. Due to the hard and brittle characteristics of iron castings, it is determined that tools are more expensive than ordinary steel. With the advancement of cutting technology and the development of tool materials, how to choose tool materials has become one of the considerations of machining technicians. MOOKTOOL tool engineers Combining the processing experience in the iron casting industry, summing up the experience from the high-speed cutting and high-hardness cutting tools, it is a good idea.
Iron castings include gray cast iron, nodular cast iron, vermicular graphite cast iron, white cast iron and various alloy cast irons; in terms of machinability, gray cast iron, pearlitic nodular cast iron and some alloy cast irons are free-cutting materials; and vermicular graphite Cast iron, white cast iron and high alloy wear-resistant cast iron (such as high nickel-chromium alloy cast iron with hardness HRC60) are difficult to cut materials.
Gray cast iron has always been one of the main raw materials for the automobile manufacturing industry. It is used to manufacture various parts, including engine blocks, cylinder heads, differential cases, shafts, flywheels, brake drums and brake discs. The absolute amount of gray cast iron in the automobile manufacturing industry is surprisingly large, and MOOKTOOL cubic boron nitride tools are undoubtedly the most successful application in gray cast iron processing. In addition, cubic boron nitride tools have been proven to be efficient and low-cost cutting tools in the processing of high-hardness cast iron parts such as various chilled cast iron, wear-resistant alloy cast iron, and white cast iron. However, in the processing of nodular cast iron and vermicular graphite cast iron, due to the affinity of cubic boron nitride tools and free ferrite, further research is still needed. For the processing of high-strength nodular cast iron, MOOKTOOL introduced CBN, which is compared with ordinary alloy tools. Astonishing tool life, the cost of the tool spread to each workpiece is greatly reduced, and the processing efficiency can be increased several times.
1. Material of tool for grey cast iron processing
Although the application of nodular cast iron and vermicular graphite cast iron is increasing, the application of gray cast iron is still strong. In the automobile manufacturing industry, a large amount of gray cast iron processing (especially brake drums and brake discs) will continue to be retained. However, today’s processing conditions have been different from the past. Due to the use of cubic boron nitride tools, the cutting speed has increased by approximately 335m/min compared to 10 years ago. The higher temperatures generated by high-speed cutting may dissolve the coated carbide of the cutting insert in a manner very similar to the chemical reaction between cubic boron nitride tools and ferrite. Cast iron workpieces are hard and brittle. When turning cast iron workpieces, CNC blades need to withstand higher cutting heat and cutting force. At present, most CNC blades for turning cast iron workpieces are carbide-coated blades, and the thickness of the coating is generally 8 microns– The 20 micron, coated CNC blades expose the alloy body after the coating collapses when encountering casting defects, which causes the low durability of the coated carbide CNC blades when turning cast iron workpieces.
Cubic boron nitride tools specially designed for high-speed machining of gray cast iron (cutting speeds up to 550m/min) have been put on the market. These cubic boron nitride tools for high-speed cutting can maintain high wear resistance for a long time to improve productivity). In the machining test (cutting speed range: 400-1658m/min) of rough machining gray cast iron brake disc parts using the new CBN cubic boron nitride tool, the tool life is doubled compared with the use of silicon nitride ceramic inserts. Productivity has increased by 20-200%. This increase in productivity is due to the better cutting edge toughness of MOOKCBN cubic boron nitride tools, allowing it to use higher feed rates than ceramic inserts.
2. Machining tools for ductile iron and vermicular graphite iron
Although the polycrystalline cubic boron nitride tool has been proven to be an excellent cutting tool material, it can achieve almost infinite tool life when cutting gray cast iron. Unfortunately, the use of cubic boron nitride tools to process ductile cast iron and vermicular graphite cast iron will be affected by chemical dissolution. In these processes, the tool material interacts with the higher iron content of cast iron, which can cause rapid tool wear. This problem has promoted the need to develop a tool grade that can withstand chemical effects. CBN is developed in response to the above-mentioned ductile iron processing mechanism. It is often used for high-speed cutting of pearlitic ductile iron, such as QT500, QT600, QT700, QT800, QT900 and other high-strength and strong graphite cast irons.
In order to process these new cast iron materials, tools are required to have both improved wear resistance and very good toughness-and it is difficult to balance these two properties at the same time. In order to meet this challenge, many tool manufacturers are working hard to develop tools that can provide the best combination of these two properties.
3. High hardness and wear-resistant cast iron machining tools such as Ao Bei ductile iron and white cast iron
Ao Bei Ductile Iron is a new type of wear-resistant alloy cast iron. The current high-grade normalized QT800-6 and QT900-6, and austempered ductile iron ADI are the veritable “Ginseng Iron”! White cast iron As early as the Spring and Autumn Period, China made white cast iron with good abrasion resistance and used it as some anti-wear parts. This cast iron has the characteristics of high carbon and low silicon, high hardness, but very brittle. The most widely used is high chromium white cast iron with a chromium content of 12% to 20%. The structure is formed (cr, Fe ) 7C3 carbides. CBN tools for machining Ao Bei ductile iron and white cast iron have been proven to be reliable machining tools. White cast iron also contains high chromium white cast iron (referred to as high chromium cast iron), medium chromium, low chromium white cast iron, as well as common common cast iron containing white cast iron. MOOKTOOL, as a pioneer in the super-hard tool industry, has a strong influence on cast iron materials. The research on machining and tool materials has been far ahead, and the non-metallic binder CBN tool material (MOOKCBN tool) has been launched with a balanced grinding performance. Commonly used in high alloy cast iron processing fields, such as high chromium alloy cast iron, high nickel chromium chilled cast iron, austempered ductile iron, high silicon chromium molybdenum alloy cast iron and other materials.
The integral cubic boron nitride blade is used for intermittent turning of slurry pump parts as an example: the integral CBN blade is used to turn the outer circle of the slurry pump impeller. Since the impeller has 5 blades, it is intermittent cutting. The cutting parameters of the blade are: vc=75m/min, ap=5mm, f=0.1mm/r. During the cutting process, the tool has to withstand 5 impacts per revolution of the impeller, and one cutting edge has to withstand more than 3,000 impacts at a time. The cutting results show that there is no fracture after cutting a workpiece, and one blade is equivalent to 25 ceramic blades, which fully demonstrates its heat and impact resistance. It not only greatly reduces the cost of the tool, but also increases the production efficiency by 5 times. . Use cubic boron nitride blades to finish turning the inner hole, the hole depth is 80mm, and the cutting parameters: vc=100m/min, ap=1mm, f=0.5mm/r. The inner hole is finished with one precision turning, and the measured two ends are the same size, and there is no back-out phenomenon. MOOKCBN has good wear resistance, and the consistency of the size of the machined parts is guaranteed; while the ceramic tool fine turning needs 3 to 4 knives to complete, and the blade edge wears quickly during cutting, which increases the cutting resistance and causes the phenomenon of tool withdrawal, which has a serious impact Improve the quality of the machined surface. It can be seen that ceramic tools have lost their advantages in rough machining of high-hardness castings.
With the increasingly fierce competition in the machinery industry, how to improve the processing technology and improve the processing efficiency and reduce the overall cost through the correct selection of the material of the machining tool has become the consideration of the machining technician. As needles and brain knives, if we understand their performance and make the right choice, it can bring great benefits to the enterprise.
Please keep the source and address of this article for reprinting: Three Keys of Machining Technology of Iron Castings
Minghe Die Casting Company are dedicated to manufacture and provide quality and high performance Casting Parts(metal die casting parts range mainly include Thin-Wall Die Casting,Hot Chamber Die Casting,Cold Chamber Die Casting),Round Service(Die Casting Service,Cnc Machining,Mold Making,Surface Treatment).Any custom Aluminum die casting, magnesium or Zamak/zinc die casting and other castings requirements are welcome to contact us.
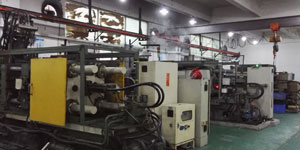
Under the control of ISO9001 and TS 16949,All processes are carried out through hundreds of advanced die casting machines, 5-axis machines, and other facilities, ranging from blasters to Ultra Sonic washing machines.Minghe not only has advanced equipment but also have professional team of experienced engineers,operators and inspectors to make the customer’s design come true.
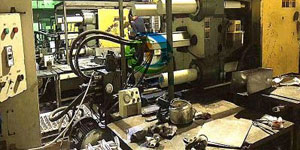
Contract manufacturer of die castings. Capabilities include cold chamber aluminum die casting parts from 0.15 lbs. to 6 lbs., quick change set up, and machining. Value-added services include polishing, vibrating, deburring, shot blasting, painting, plating, coating, assembly, and tooling. Materials worked with include alloys such as 360, 380, 383, and 413.
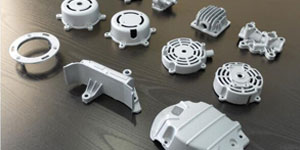
Zinc die casting design assistance/concurrent engineering services. Custom manufacturer of precision zinc die castings. Miniature castings, high pressure die castings, multi-slide Mold castings, conventional mold castings, unit die and independent die castings and cavity sealed castings can be manufactured. Castings can be manufactured in lengths and widths up to 24 in. in +/-0.0005 in. tolerance.
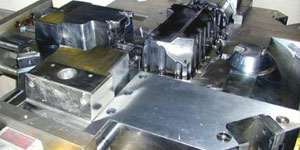
ISO 9001: 2015 certified manufacturer of die cast magnesium, Capabilities include high-pressure magnesium die casting up to 200 ton hot chamber & 3000 ton cold chamber, tooling design, polishing, molding, machining, powder & liquid painting, full QA with CMM capabilities, assembly, packaging & delivery.
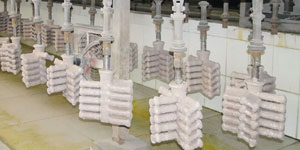
ITAF16949 certified. Additional Casting Service Include investment casting,sand casting,Gravity Casting, Lost Foam Casting,Centrifugal Casting,Vacuum Casting,Permanent Mold Casting,.Capabilities include EDI, engineering assistance, solid modeling and secondary processing.
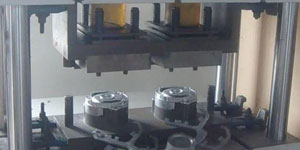
Casting Industries Parts Case Studies for: Cars, Bikes, Aircraft, Musical instruments, Watercraft, Optical devices, Sensors, Models, Electronic devices, Enclosures, Clocks, Machinery, Engines, Furniture, Jewelry, Jigs, Telecom, Lighting, Medical devices, Photographic devices, Robots, Sculptures, Sound equipment, Sporting equipment, Tooling, Toys and more.
What Can we help you do next?
∇ Go To Homepage For Die Casting China
→Casting Parts-Find out what we have done.
→Ralated Tips About Die Casting Services
By Minghe Die Casting Manufacturer |Categories: Helpful Articles |Material Tags: Aluminum Casting, Zinc Casting, Magnesium Casting, Titanium Casting, Stainless Steel Casting, Brass Casting,Bronze Casting,Casting Video,Company History,Aluminum Die Casting |Comments Off
Link to this article:Three Keys of Machining Technology of Iron Castings
Reprint Statement: If there are no special instructions, all articles on this site are original. Please indicate the source for reprinting.:Casting Wiki,THANKS!^^